Introduction: The Certainty Imperative in an Uncertain World
For any asset owner, developer, or senior project manager in the Architecture, Engineering, and Construction (AEC) industry, the decision to renovate an existing building is fraught with uncertainty. It is a well-understood truth that these projects are notorious for running over budget and behind schedule. These are not minor inconveniences; they are significant threats to profitability, asset performance, and return on investment. The core of this risk lies in a fundamental, decades-old problem: the gap between a building’s design documentation and its physical reality. This is the As-Built Dilemma.
The root cause of this uncertainty is the industry’s reliance on outdated or inaccurate as-built documentation. Traditional 2D drawings, often the only record available, frequently fail to reflect the true conditions of a structure. Undocumented modifications lead to a cascade of costly on-site discoveries, forcing teams into a reactive cycle of expensive change orders, schedule-shattering delays, and significant material waste. This chasm between the plan and the reality transforms a strategic investment into a high-stakes gamble.
In this environment, a new strategic imperative has emerged: the As-Built Digital Twin. This is not merely a new piece of software or a 3D model. It is the path to achieving certainty, control, and predictability in building renovation. A Digital Twin transcends static blueprints by creating a living, data-rich virtual replica of the physical asset. It serves as the single source of truth, a dynamic model that evolves with the building throughout its lifecycle.
This report provides a comprehensive guide for asset owners and AEC professionals on leveraging Digital Twin technology—from 3D laser scanning to a fully operational model—to transform high-risk renovations into predictable, high-value investments. It will demonstrate how this technological shift moves retrofitting from risk mitigation to strategic value creation.
Step 1: From 3D Laser Scan to Intelligent Model: The Foundation of Truth
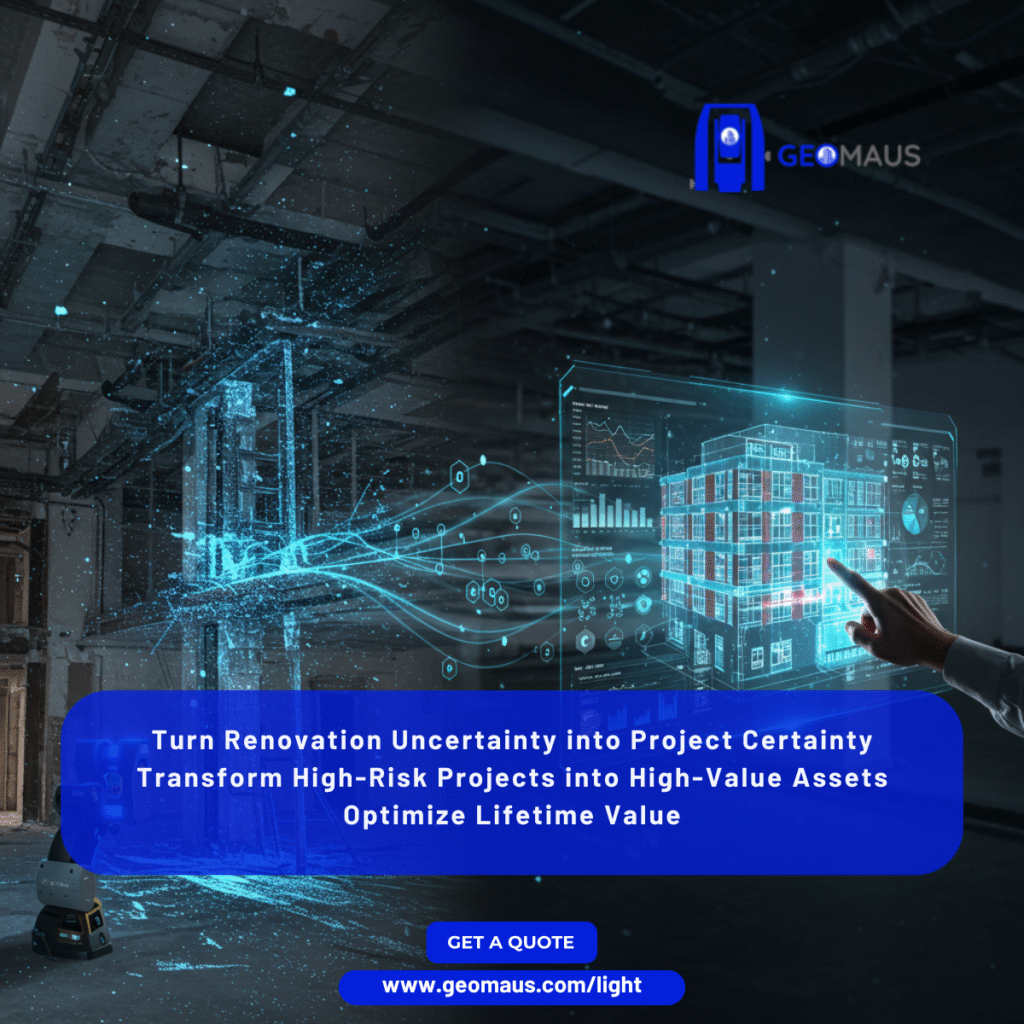
To de-risk a renovation, all stakeholders must work from a perfect understanding of the existing asset. This requires moving beyond flawed records and establishing a new baseline of reality captured with indisputable precision. This foundational stage transforms raw physical space into a structured, intelligent digital asset.
Eradicating Uncertainty with Reality Capture
The process begins with a high-fidelity 3D laser scan of the building, a technique known as reality capture. This technology uses LiDAR to create a dense and dimensionally precise “point cloud”—a complete digital record of the building’s exact geometry with millimeter-level accuracy.
This step is a direct antidote to the primary risk in any renovation: unknown conditions. Traditional manual measurements are time-consuming and prone to human error. A 3D scanner can capture an entire environment in a fraction of the time with vastly superior accuracy, a core service offered by technology providers like GeoMaus. The objective is to create as-built documentation that is a true representation of the site, eliminating the guesswork that leads to clashes, revisions, and delays.
The Scan-to-BIM Workflow: Creating an Intelligent Foundation
A point cloud is raw data. To become useful for planning, it must be transformed into a structured model through the Scan-to-BIM (Building Information Modeling) process. Specialized software converts the point cloud into a 3D model where geometric shapes are recognized as intelligent components like walls, pipes, and columns.
This process creates the firm foundation for all subsequent design, clash detection, and construction sequencing. This foundational model ensures architects and engineers design within real-world constraints, not a hypothetical version from an old blueprint, dramatically reducing the risk of design errors and costly rework.
The AI Accelerator: Revolutionizing Point Cloud Processing
A significant evolution in this stage is the integration of Artificial Intelligence (AI) and Machine Learning (ML). Historically, converting a point cloud into a structured BIM model was a manual, labor-intensive task.
Today, AI algorithms automate this critical step. Trained on vast datasets, machine learning models can analyze a point cloud and automatically identify and classify architectural and structural elements with minimal human intervention. AI also excels at data cleanup, filtering out “noise” from reflective surfaces or dust to produce a cleaner, more reliable dataset.
This AI-driven automation dramatically reduces the time, cost, and potential for error in creating the foundational BIM model, making the Digital Twin proposition more accessible and economically viable. The output is not just a static model but a pre-populated, semi-intelligent asset database, which fundamentally improves the economics and timeline of Digital Twin adoption. By lowering the upfront cost and time commitment, AI makes it easier for organizations to take the first crucial step toward predictable, data-driven renovation outcomes.
Step 2: The Leap to a Living Asset: Evolving BIM into a Digital Twin
A high-fidelity BIM model is a monumental step forward, but it is a perfect snapshot in time. The true quantum leap in value occurs when this static foundation evolves into a living, breathing Digital Twin. This requires a new layer of technology and strategic data integration, turning the digital blueprint into a dynamic replica that mirrors the building’s operational life.
What’s the Difference? Static Model vs. Dynamic Twin
It is critical to distinguish between a BIM model and a Digital Twin. A BIM model is a static, 3D representation of a building’s characteristics. A Digital Twin, by contrast, is a
dynamic virtual replica connected to its physical counterpart through a continuous, two-way flow of data. It starts with the BIM model but then integrates real-time operational data, meaning it is not just a model
of the building but a living simulation with the building.
The Tech Behind the Twin: IoT, CDEs, and Analytics
Evolving a BIM model into a Digital Twin involves creating an integrated ecosystem:
- IoT (Internet of Things) Sensors: These are the sensory organs, deployed on critical assets like HVAC units and pumps to collect real-time data on temperature, energy use, vibration, and more.
- Data Integration Framework (Common Data Environment – CDE): This centralized platform is the brain, ingesting and harmonizing data from the BIM model, IoT sensors, and other building systems (like a BMS or CMMS).
- Visualization & Analytics Engine: This engine makes data actionable. It visualizes real-time data on the 3D model (e.g., a red glow on a failing HVAC unit) and runs advanced analytics to detect patterns, predict future states, and generate insights for optimization.
A Practical Guide to Creating Your Digital Twin
For asset owners, the process can be broken down into a logical sequence:
- Define Objectives and Scope: Start with clear business goals. Do you want to reduce maintenance costs by 20% or achieve LEED certification? Goals define the scope.
- Identify Physical Components and Data Sources: Map every component to be monitored and catalog all data sources, from new IoT sensors to existing utility meters.
- Data Capture and Foundational Modeling: Leverage the work from Step 1. The intelligent Scan-to-BIM model is the foundation of the Digital Twin.
- Data Integration and Synchronization: This is where the static model becomes a live twin. Connect data sources to their corresponding assets in the BIM model using the CDE, establishing reliable data pipelines.
- Implement Real-Time Monitoring and Analytics: Configure dashboards for KPIs, set alert thresholds for anomalies, and deploy machine learning algorithms for predictive analytics.
- Iterate and Refine: A Digital Twin is a living system. It must be continuously updated as the physical building changes, and its analytical models will improve as they are fed more data.
The true value of a Digital Twin emerges when it becomes the central operational hub for a building, breaking down the data silos that have traditionally plagued facility management. This integrated approach also democratizes building data, translating complex sensor readings into intuitive, visual information that empowers a wider range of stakeholders to make better, faster decisions.
Step 3: The Digital Twin at Work: Maximizing Lifetime Asset Value
Once operational, the Digital Twin becomes a powerful engine for value creation, optimizing operations, managing costs, and enhancing the asset’s long-term performance.
Predictive Maintenance: From Reactive to Proactive
One of the most immediate financial impacts is the shift to predictive maintenance (PdM). The traditional “run-to-failure” approach is inefficient and costly. The Digital Twin changes this by continuously monitoring key performance indicators. AI algorithms analyze this data to predict impending failures weeks or months in advance, automatically generating work orders.
A case study from the Papa Giovanni XXIII school in Italy illustrates this power. A Digital Twin monitoring the HVAC system led to a 20% improvement in system reliability and a 15% reduction in energy consumption. This aligns with industry findings that PdM can reduce maintenance costs by up to 30% and cut unexpected breakdowns by as much as 70%.
Energy Optimization: Simulate Before You Spend
Meeting modern energy efficiency standards is a major challenge for older buildings. The required capital investment is substantial, and the ROI is often uncertain. The Digital Twin acts as a virtual, risk-free testbed for these investments. Asset owners can simulate the impact of various Energy Conservation Measures (ECMs)—like installing a new chiller or upgrading windows—to get highly accurate forecasts of energy savings and financial returns before committing capital.
The renovation of Keppel Bay Tower in Singapore provides a powerful example. A Digital Twin was used to test potential ECMs. The implementation of just eight low- or no-cost measures resulted in a 7% energy efficiency improvement, contributing to an overall 30% reduction in annual energy consumption and annual electricity cost savings of approximately $400,000. Other studies show Digital Twin-driven optimization can reduce HVAC energy use by 23-39% and lighting costs by up to 79%.
Enhanced Safety, Security, and Occupant Experience
Beyond maintenance and energy, the Digital Twin unlocks further value:
- Safety and Emergency Response: By integrating with fire detection systems, the twin can run real-time simulations of fire and smoke propagation to identify the safest evacuation routes.
- Security and Access Control: Integration with security systems provides a comprehensive, real-time view of the facility, monitoring access points and flagging anomalies.
- Occupant Experience and Space Optimization: The twin can monitor indoor environmental quality (CO2, temperature, etc.) to optimize for occupant health and comfort. It can also analyze space utilization data to inform better layouts and prevent investment in underused areas.
This simulation capability transforms capital planning from a high-stakes decision based on estimates to a strategic financial exercise. A board can “test drive” multiple retrofit scenarios, compare their long-term ROI, and allocate capital with maximum confidence. This creates a continuous improvement loop—Monitor, Simulate, Renovate, Update, Optimize—that adds value throughout the building’s lifecycle.
The Unmistakable Business Case: Quantifying Your Digital Twin ROI
While the technology is impressive, its adoption hinges on a clear business case. A Digital Twin doesn’t just make a building smarter; it makes it a more valuable, predictable, and profitable asset.
A Paradigm Shift in Asset Valuation
The existence of a comprehensive Digital Twin fundamentally increases the intrinsic value of a building. It acts as a perfect “digital logbook,” containing a complete history of design, renovations, maintenance, and performance data. When the building is sold, this digital asset can be transferred to the new owner, eliminating information asymmetry and de-risking the acquisition. This transparency can command a significant market premium and lead to faster leasing cycles.
Financial Breakdown: Traditional vs. Digital Twin Retrofit
The following table contrasts the financial implications of a traditional renovation with a modern, Digital Twin-led retrofit, demonstrating that the Digital Twin approach delivers substantially lower total lifecycle costs and a higher return on investment.
Metric | Traditional Renovation (The Gamble) | Digital Twin-Led Retrofit (The Certainty) | Financial Impact |
Upfront Surveying & Documentation | High manual labor costs; time-consuming and prone to error. | Automated 3D laser scanning; fast and highly accurate. | Reduced labor costs and project initiation time by capturing all data in a fraction of the time required by manual methods. |
Rework & Change Order Costs | High risk; typically 10-15% or more of total project cost due to on-site discovery of discrepancies. | Near-zero risk; clashes are detected and resolved in the digital model before construction begins. | Significant cost avoidance by eliminating the primary source of budget overruns and material waste. |
Project Timeline & Delays | High risk of schedule overruns due to unforeseen conditions and subsequent redesign. | Predictable schedule; design is based on perfect as-built data, minimizing surprises. | Increased certainty in project delivery dates, reducing financing costs and enabling earlier revenue generation from tenants. |
Annual O&M Costs (Post-Renovation) | Reactive maintenance model; typically 1.5% of asset value annually. Higher emergency repair costs. | Predictive maintenance model; typically 1% of asset value annually. Maintenance costs can be reduced by up to 30%. | Substantial and recurring annual operational savings through proactive, condition-based maintenance instead of reactive repairs. |
Annual Energy Costs (Post-Renovation) | Standard performance, often with a “performance gap” where savings are less than designed. | Optimized performance; energy savings of 15-30% or more are achievable and verifiable. | Lower utility expenditures and enhanced sustainability credentials. Documented savings of $400,000 annually in case studies. |
Asset Lifecycle & Capital Planning | Standard equipment lifespan; capital replacement is based on age and failure. | Extended equipment lifespan due to predictive maintenance. Capital planning is data-driven. | Deferred capital expenditures and optimized long-term capital planning, improving the asset’s net present value. |
Long-Term Asset Value & Leaseability | Standard market value. | Premium market value; higher leaseability due to proven efficiency, sustainability, and enhanced tenant experience. | Increased asset valuation and attractiveness to sophisticated tenants and buyers, leading to higher sale prices and lower vacancy rates. |
This framework repositions the Digital Twin from a technological feature to a core financial strategy, providing a tangible tool for C-suite executives to justify the investment.
GeoMaus as the End-to-End Partner
Successfully navigating this shift requires a partner with expertise across the entire Digital Twin lifecycle. GeoMaus provides the full, integrated suite of services and software required to make this process seamless. This begins with world-class 3D laser scanning and reality capture, extends through expert Scan-to-BIM conversion accelerated by AI, and culminates in a bespoke, cloud-based software platform that serves as the operational Digital Twin. This end-to-end capability ensures the journey from physical asset to intelligent Digital Twin is efficient, reliable, and delivers maximum value.
Get Your Free Quote: Geomaus.com/light
Conclusion: Swap the Gamble for a Guarantee
The “As-Built Dilemma” has for too long forced asset owners to treat renovation as a financial gamble. The adoption of a comprehensive Digital Twin strategy marks a definitive end to this era of uncertainty. By starting with a foundation of absolute truth and evolving it into a living, data-driven replica, the Digital Twin introduces certainty, control, and predictability into every phase of a building’s lifecycle.
Mastering the renovation of our existing building stock is one of the most critical challenges facing the AEC industry, essential for meeting sustainability targets and creating healthier, more efficient environments. Digital Twins are the key to unlocking this potential at scale.
The journey from high-risk gamble to high-value investment is a practical reality. For asset owners and developers ready to move beyond the limitations of the past, the time to act is now. This requires a strategic partner who understands both the technological complexities and the business imperatives. We invite you to contact GeoMaus for a consultation to build a tailored business case for your next renovation or retrofit project. Together, we can transform your next significant risk into your next resounding success.